بومی سازی ۸ فناوری مهم در صنعت فولاد
بومیسازی حداقل ۸ فناوری مهم در صنعت فولاد و معادل ۶۰۰میلیون دلار قطعه و تجهیز در یک سال، کاهش ۵۰درصدی وابستگی ارزی و افت ۱۰میلیونتنی نیازهای وارداتی صنعت فولاد نشان داده است که مهندسان ایرانی ید طولایی در شکست تحریم دارند.
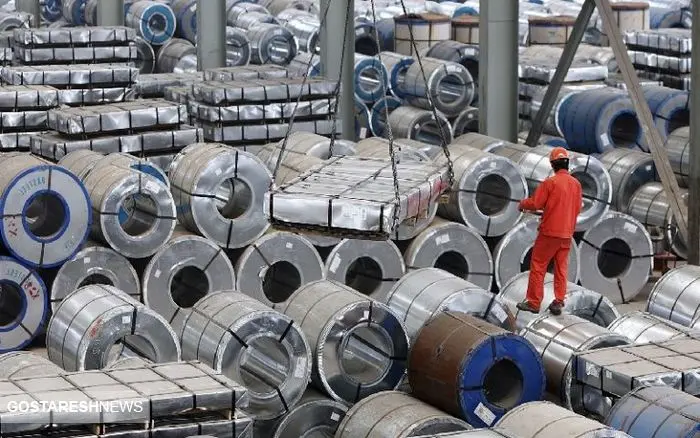
۲۸ آبان سال ۹۸ جلسه مهمی با حضور ۲۵۰۰ نفر از تولیدکنندگان، کارآفرینان و فعالان اقتصادی در حضور امام خامنهای برگزار گردید که نکات مهمی در باب تحریم و تولید در آن جلسه از سوی مقام معظم رهبری مطرح شد.
شاهبیت سخنان رهبری در آن جلسه از این قرار بود که "این تحریم فعلاً خواهد بود؛ اینکه کسی امید ببندد به اینکه حالا یک سال دیگر، دو سال دیگر این تحریم تمام میشود، خیال باطل است، این تحریم حالاحالاها هست،کار اساسی مصونسازی اقتصاد کشور از آسیب دیدن از تحریم است، باید کاری کرد که ما در مقابل تحریم آسیبپذیر نباشیم. تولید بایستی در کشور پیشرفت پیدا کند؛ علاج کار این است. اگر توانستیم با تکیهی بر توان داخلی، تحریم را بیاثر بکنیم، آن عامل تحریمکننده هم از تحریم دست برمیدارد؛ یعنی او هم وقتی فهمید تحریم فایدهای ندارد، از تحریم دست برمیدارد."
حال که یک سال از آن جلسه مهم میگذرد و اقتصاد کشور درگیر تحولات گسترده شده است، گروه اقتصادی درپی آن آمده است که در راستای امیدافزایی، نمونههای موفق در کشور را که اتفاق افتاده و تحریم را بیاثر کرده است، بازگو نماید.
در این بخش به نمونههایی از شکست تحریم در صنعت فولاد میپردازیم.
صنعت فولاد در کشور ما جزو صنایعی است که علیرغم تحریمهای شدیدی که طی سالهای گذشته علیه این صنعت، اعمال شد ولی توانسته است با مقابله با این تحریمها و تکیه بر توان فنی مهندسی داخلی پیشرفتی خیرهکننده داشته باشد و در حالی که در سال ۸۶ ایران بعد از آمریکا دومین واردکنندۀ خالص فولاد در جهان بود، امروز دهمین صادرکننده فولاد شد.
در بخش بومیسازی قطعات و کاهش ارزبری هم طی این سالها، روی بومیسازی بیش از ۱۹ هزار قطعه در این صنعت کار شد و طی یک سال اخیر، معادل ۶۰۰ میلیون دلار قطعه و تجهیز در صنعت فولاد بومیسازی شده است. همچنین طی دو سه سال گذشته ۱۱۰ دلار بهازای تولید هر تُن فولاد وابستگی ارزی داشتیم که در زمان حاضر این عدد به نصف رسیده است و نیاز ۱۱.۵میلیونتنی در واردات به حدود ۱میلیون تن کاهش یافت.
بومیسازی تولید آهن اسفنجی بهروش احیای مستقیم و گندلهسازی، تولید الکترود گرافیتی، داخلیسازی فناوری ساخت تبدیل کک سوزنی، نیل به فناوری ساخت کورههای ذوب القایی با ظرفیت ۱۰۰ تا ۱۵۰ تن، فعالسازی دستگاههای گیربُکس با قدرتهای بالا با موتور ۱۵ مگاوات، داخلیسازی زنجیرهای مصرفکنندۀ قطعات یراقآلات و پیچومهره، خودکفایی در تولید نسوزها و سیستم انتقال موادودستیابی به تکنولوژی احیای لجن آهن اسفنجی بخشی از دستاوردهای مهم صنعت فولاد در مقابله با تحریم است.
صنعت فولاد با برنامه تولید الکترود گرافیتی که فاز نخست آن آماده بهرهبرداری است، میتواند نیاز این صنعت به این مواد اولیه را به صفر برساند. موفقیت در تولید الکترود گرافیتی در حالی به وجود آمده است که فناوری ساخت تبدیل کک سوزنی تا پیش از این تنها در انحصار ژاپن و آمریکا بود و تولید الکترود گرافیتی را نیز کشورهای معدودی در اختیار دارند، اما دانش تولید این ماده مهم بهدست متخصصان و دانشمندان ایرانی در صنعت فولاد بومیسازی شد. کاهش وابستگی صددرصدی کشور به الکترود گرافیتی وارداتی، از جمله مسائلی بود که ذهن تولیدکنندگان فولاد را به خود مشغول کرده بود وخوشبختانه اکنون با تولید کُک سوزنی بهعنوان ماده اولیه تولید الکترود گرافیتی در کشور، این نگرانی رفع شده است.
*از تحریم استقبال نمیکنیم، ولی فرصت است
برای گفتگو در خصوص نمونههایی از موفقیت صنعت فولاد در شکست تحریم بهسراغ سید رسول خلیفه سلطانی دبیر انجمن تولیدکنندگان فولاد و رضا شهرستانی عضو انجمن فولاد رفت.
خلیفه سلطانی در این گفتگو به جزئیات اقدامات انجامشده در حوزه بومیسازی صنعت فولاد پرداخت و با اشاره به اینکه مسلماً تحریم چیز خوبی نیست، گفت: اما در عین حال از دلِ هر تهدیدی، فرصتهایی زنده میشود؛ ما زمانی که تحریم نبودیم، فرصتهایی را از دست دادیم که باید برای جبران آنها اقدامات اساسی را انجام دهیم.
وی افزود: ما کشوری هستیم که وقتی ارز نفت را به دست میآوریم، در خارج از ایران سرمایهگذاری نمیکنیم و ارز داخل کشور تزریق میشود. تجربه ثابت کرده همیشه میزان ارز نفتی که وارد اقتصاد کشور شده است، فراتر از نیاز اقتصاد بوده و منجر به بروز بیماری هلندی در اقتصاد شده است.
عضو انجمن فولاد با بیان اینکه بیماری هلندی برای کشورهایی است که تراز تجاری مثبت آنها وارد کشور میشود، تصریح کرده است: این موضوع ارزش پول ملی را بالا برده و کشور خواهناخواه وارداتچی شده است. در این دوران به تولیدکننده آسیبهای جدی وارد میشود زیرا وقتی ارزش پولی ملی بالا است، واردات نسبت به صادرات و تولید داخل بصرفهتر است، یعنی شما یک جنس را از خارج نسبت به جنس داخلی با قیمت ارزانتر وارد میکنید و واردات آن نسبت به تولید آن در داخل ارزانتر است. در این اوضاع صادرات دیگر نمیتواند وجود داشته باشد و ما فقط وارداتچی نفت میشویم؛ اینها تئوری یا داستان نیست و واقعیت محض است که در کشور اتفاق افتاده است.
خلیفه سلطانی اضافه کرد: امروز تراز تجاری ما منفی است، یعنی نیاز ما به ارز، بیشتر از آن چیزی است که میتوانیم تولید ارز کنیم. در حال حاضر ارزش پول ملی ما کاهش پیدا کرده این در حالی است که در ایدهآلترین حالت نباید ارزش پولی ملی آنقدر بالا باشد که ما وارداتچی شویم و نه آنقدر ارزش پولی ملی پایین بیاید که ما نتوانیم نیازهای داخلیمان را تامین کنیم.
وی با تأکید بر اینکه تحریم چیز خوبی نیست ولی در لببه لبِ تراز تجاری مثبت زندگی کردن چیز خوبی است، گفت: در شرایط فعلی که با تهدید تحریم مواجه هستیم از آن می توانیم به عنوان یک فرصت ویژه استفاده کنیم. امروز ارزش پولی ملی ما پایین آمده و ما به عنوان تولیدکننده فولاد باید از این فرصت استفاده کنیم، باید به یک حد تعادل و عدم تحریم برسیم. اما دقت کنیم اگر یک روز تحریم ها لغو شد، نباید دوباره درگیر ریخت و ریزهای ارزی شویم.
*راه اندازی سامانه بومیسازی ۱۹ هزار قطعه در صنعت فولاد/ ۶۰۰ میلیون دلار قطعه بومیسازی شد
خلیفه سلطانی با اعلام اینکه باید از تحریم به گونه ای استفاده کنیم که در شرایط بدون تحریم که درآمد ارزی بالایی داریم بتوانیم این ارز را خارج از کشور سرمایهگذاری کنیم، تصریح کرد: امروز قطعات و تجهیزاتی که نیاز صنعت فولاد است را نمی توانیم وارد کنیم و این یک فرصت است و ما در انجمن فولاد با کمک دستگاههای حاکمیتی که عمدتاً وزارت صمت است با تهیه برنامه هایی در صدد استفاده از فرصت تحریم ها هستیم.
دبیر انجمن تولیدکنندگان فولاد ایران با اشاره به نهضت بومیسازی در صنعت فولاد که طی چند سال گذشته آغاز شده است، گفت: وقتی بوی تحریم آمد، ما اولین جشنواره بومیسازی را سه سال پیش برگزار کردیم. علاوه بر آن یک سامانه بومیسازی نیز راه اندازی شده که در آن بومیسازی ۱۹ هزار قطعه بارگذاری شده است.
وی با اعلام اینکه راه اندازی این سامانه یک سال طول کشید، افزود: چیزی حدود ۶۰۰ میلیون دلار، از ابتدای سال تاکنون در کشور بومیسازی قطعات و تجهیزات در صنعت فولاد انجام شده است. باید تأکید کنم نهضت بومیسازی در تمام ارکان صنعت فولاد ریشه دوانده است، در تمام شرکتها یک نهضت بومیسازی راه افتاده و در نمایشگاه دائمی بومیسازی و سایت های مربوطه شرکت ها می توانند توانمندی ساخت داخل تجهیزات و قطعات را بارگذاری کنند.
*ایجاد صندوق پژوهش و فناوری فولاد میان تولیدکنندگان و تأمین کنندگان قطعات و تجهیزات
خلیفه سلطانی با اشاره به تلاش تولیدکنندگان در بومی سازی قطعات مخصوصا قطعات سنگین، گفت: ما یک صندوق پژوهش و فناوری فولاد با مشارکت ایمیدرو و انجمن فولاد راه اندازی کرده ایم، به این صورت که همه شرکتهای فولادی در آن صندوق دارای یک سهم هستند و این صندوق با سرمایۀ اولیه صد میلیارد تومانی تا پایان امسال با توجه ارکانش اعلام موجودیت خواهد کرد. این صندوق پژوهش و فناوری یک حلقه ارتباطاتی میان تولیدکنندگان و تامینکنندگان است. به عبارتی مشوق هایی برای بومی سازی قطعات در صنعت فولاد در نظر گرفته شده است و سعی ما این است که کمتر تسهیلات بدهیم و بیشتر سعی می کنیم گرفتاریهای اعتباری آنها مانند ضمانتنامه را حل کنیم.
وی افزود: از کارهای دیگر صندوق، بحث تسهیلات ارزانقیمت است که در قالب این صندوق داده میشود، طبق مقررات صندوقهای پژوهش و فناوری، که تحت حمایت معاونت علمی، ریاستجمهوری و صندوق نوآوری و شکوفایی هستند، ما به ازای صد میلیارد تومان سرمایهای که اینجا ثبت میشود، ۹ برابر آن اعتبار می دهیم.
* وابستگی ارزی ۱۱۰ دلاری در تولید هرتن فولاد امروز نصف شد
این عضو انجمن فولاد افزود: مهمترین شاخصه برای یک کار خوب، نظام اطلاعاتی است، یعنی اطلاعات به صورت رقابتی باید در اختیار همه قرار گیرد، در بومی سازی باید مشتری ها مشخص و نیاز سنجی واحدها بررسی شود در نهایت بتوان به دستاورد مناسبی دست پیدا کرد. در شرایط رقابتی بحث بر سر کیف و قیمت است و همین امر یک تنازع بقا را شکل می دهد، تا تنازع بقا نباشد اهداف بومیسازی محقق نخواهد شد.
وی با تأکید بر اینکه قلب تپندۀ بومیسازی نظام اطلاعاتی است، اظهار داشت: طی دو سه سال گذشته ۱۱۰ دلار به ازای هر تُن فولاد وابستگی ارزی داشتیم که در حال حاضر این عدد به نصف رسیده است. البته این عدد باید کاهش بیشتری پیدا کند. یک زمانی وقتی یک تولیدکننده در صنعت فولاد از داخلی سازی صحبت می کرد، باورپذیر نبود، اما امروز همه باور دارند.
خلیفه سلطانی گفت: امروز در صنعت فولاد نه تنها بومیسازی می کنیم بلکه صاحب تکنولوژیهایی هستیم که میتوانیم برای بار اول در دنیا مطرح کنیم. کورههای القایی که ما به تکنولوژی آن دست پیدا کرده ایم بسیار حائز اهمیت است، در این بخش کوره های القایی بیشتر از ۵۰ تن نداریم اما ما میتوانیم با تکنولوژیهای که به دست آورده ایم به ۱۰۰ تا ۱۵۰ تن هم برسیم.
در بخش نورد هم دستگاههای گیربُکس با قدرتهای بالا، به موتور ۱۵ مگاوات نیاز دارند تا یک ورقِ با عرض بالا را تولید کنند اما یک موتور ۱۵مگاوات را هیچ کس در ایران نمیسازد و کسی هم نمی فروشد. در همین زمینه پژوهشگران ایرانی به جای اینکه از یک موتور استفاده کنند از ۶ موتور به صورت همزمان استفاده می کنند تا به مگاوات مورد نیاز خود در تولید ورق ها با عرض بلند دست پیدا کنند.
کورههای ذوب القایی همان طور که از نامش مشخص است برای ذوب فلزات به کار میروند. این کورهها با اعمال میدان الکترومغناطیس از طریق سیم پیچ مسی به فلزات داخل کوره دمای آن را به سرعت افزایش داده و تا دمای ذوب می رساند. فناوری ساخت این دستگاه تا چند سال پیش در دست چند کشور بود که خوشبختانه اکنون کشورمان به تولید کننده کورههای ذوب القایی تبدیل شده است. البته فناوری ساخت کورههای ذوب القایی با ظرفیتهای پایین در اختیار چندین کشور خاص بود ولی ساخت این دستگاهها با ظرفیت بالا عمدتا در دست شرکتهای آلمانی و آمریکایی بود بنابراین شرکتهای فولاد داخلی برای تهیه این تجهیزات به کشورهای اروپایی وابسته بودند که با آغاز تحریمها و عدم فروش آن به ایران، داخلی سازی این کوره ها در اولویت تولیدکنندگان کشور قرار گرفت.
مطابق آمار در سال حدود ۵ میلیون تن تولید فولاد از طریق کوره های القایی در بیش از ۱۰۰ شرکت تولید می شوند. در این بخش حدود ۳ هزار میلیارد تومان سرمایه گذاری انجام شده که دیگر نیاز واردات آنها نداریم.به نحوی که به صورت متوسط حداقل ۳۰۰ کوره در کشور نصب و نیاز واردات را به نصف رسانده است.
تنظیم اتوماتیک حداکثر توان و حذف توان راکتیو، راندمان بالا و انطباق با استانداردهای جهانی و استفاده از یوکهای آب خنک با راندمان الکتریکی بالا از جمله ویژگیهای این کورهها هستند.
*نیاز ۱۱.۵ میلیون تنی در واردات را به حدود ۱ میلیون تن رساندیم
خلیفه سلطانی در ادامه این گفتگو با اشاره به اینکه نیاز ما فقط قطعات و تجهیزات نیست، افزود: یکی از نیازهای ما تکنولوژی است، تکنولوژی یعنی خط تولید. خوشبختانه در خطوط تولید در تکنولوژی تولید آهن اسفنجی و گندلهسازی به توانایی خوبی رسیده ایم. البته باید این مساله را مورد توجه قرار داد که فولادسازان یا پتروشیمی ها دامنۀ تنوع محصول زیادی دارند و اینطور نیست که وقتی میگوییم خودکفا میشویم، در همۀ اقلام خودکفا شده ایم. طبیعی است که هنوز در بعضی اقلام به خودکفایی نرسیدیم و وارد میکنیم. در سال ۸۶ حدود ۱۱.۵ میلیون تن واردات داشتیم که این رقم منهای صادرات بود. اما امروز واردات ما حدود ۱ میلیون تن است. امسال هم ۵۰۰ هزار تن و حداکثر ۱ میلیون تن اقلامی را واردات میکنیم که ساخت داخل ندارد که اگر شما بخواهید کارخانه آن را ایجاد کنید توجیه پذیر نیست، مگر اینکه بخواهیم صادرات کنیم و چون رقابت سنگینی وجود دارد معمولاً باید در داخل به خودکفایی برسیم و بعد بتوانیم صادرات انجام دهیم.
وی افزود: چند سال پیش کارخانجات فولادی باید تعطیل میشدند چون ورق را از خارج ارزانتر وارد میکردند. میلگرد و شمش به شدت ارزانتر بود. اما در حال حاضر صادرات شمش و آهن اسفنجی به صرفه است، یعنی محصولات میانخطی و زنجیرهای ما به صرفه است که صادر کنیم، سنگآهن، گندله، کنسانتره، آهن اسفنجی، شمش و همۀ اینها به صرفه است که صادر کنیم، یک زمانی به صرفه نبود که شما محصول نهایی را صادر کنید و یا اصلاً آن را تولید کنید. در سال ۸۶ ایران بعد از آمریکا دومین واردکنندۀ خالص جهان در فولاد بود و کسی نمیتوانست در داخل تولید کند اما امروز دهمین صادرکننده هستیم، تازه با این چوب لای چرخی که وزارت صمت گذاشته است به نحوی که اگر مشکلات نبود حتی جایگاه بالاتری داشتیم.
*زنجیره مصرفکنندۀ قطعات یراقآلات و پیچ و مهره داخلیسازی شد
خلیفه سلطان اضافه کرد: یک زمان صنعت پیچ و مهرهسازی در کشور ضعیف بود و تمام مواد اولیه آن از خارج وارد میشد، اما امروز زنجیره آن بومی سازی شده است و مواد اولیه آن فولادی است که در داخل دارد تولید میشود. کارخانجات زنجیرهای مصرفکنندۀ قطعات یراقآلات و پیچ و مهره، همۀ داخلیسازی شدند، پیچی که در ماشین پراید و پژو و دنا و تمام ماشینهایی که ساخت داخل است، اینها پیچهای معمولی نیست و هر کدام از آنها یک قطعه محسوب میشود، تمام آنها داخلیسازی شد و اینها فرصتهایی بوده که تحریم برای ما به وجود آورده است.
* شهرستانی: خودکفایی در تولید نسوزها و سیستم انتقال مواد محقق شد
در همین زمینه رضا شهرستانی عضو انجمن فولاد هم با اشاره به اینکه بومی سازی در صنعت فولاد از ۱۵ سال پیش در دستور کار قرار گرفته است می گوید: از آن سال اقدامات تدریجی برای بومی سازی قطعات و مواد مورد نیاز صنعت فولاد آغاز شد اما در سالهای اخیر با تشدید تحریم ها عزم جدی خود را برای بومی سازی قطعات و استفاده از فرصت تحریم ها برای ارتقای توانمندی داخلی آغاز کردهایم.
وی با اعلام اینکه با تدوین یک برنامه نیازمندیهای صنعت فولاد در بخش های مختلف مورد شناسایی قرار گرفت، گفت: در این برنامه تامین کننده های داخلی و نیاز شرکتها مشخص شد که براساس آن توانستیم ضمن تحلیل وضعیت صنعت، نیازمندی های وارداتی را تقسیم بندی و برنامه ها را برای داخلی سازی آنها انجام دهیم.
این عضو انجمن صنعت فولاد افزود: به عنوان نمونه در بخش نسوزها توانستیم بخشی از نیاز را بومی سازی کنیم چرا که به ازای تولید هر تن فولاد ما نیازمند یک تن مواد نسوز هستیم. برهمین اساس تولید ۳۰ میلیون تن فولاد ما نیازمند ۳۰ میلیون تن نسوز هست که با داخلی سازی ها بخشی از نیاز خود را در این بخش تامین کرده ایم.
*بومیسازی تولید آهن اسفنجی و نسوزها در صنعت فولاد
اکسید آلومینیوم (Al۲O۳) مهمترین ماده اولیه تولید نسوز است و تمامی نسوزها بر اساس درصدهای مختلفی از اکسید آلومینیوم تولید میشوند. با این حال، اکسید آلومینیوم با درصد بالا متاسفانه در کشور طی سالهای گذشته تولید نمیشد اما خوشبختانه برخی از شرکتها با توجه به تحریمها و نیاز کشور به این ماده حیاتی، به تولید اکسید آلومینیوم با خلوص بالا وارد شدهاند.
بر همین اساس برخی از معادن حاوی اکسید آلومینیوم که پیش از این غیر فعال بودند، طی سالهای ۱۳۹۷ و ۱۳۹۸ فعال و با فعالسازی این معادن، خوراک تولیدکنندگان اکسید آلومینیوم تامین شده است با این دستاورد تولیدکنندگان توانستند بخشی از نیاز صنایع کشور به این ماده را تامین کنند.
نسوز یکی از اقلام مهم در صنعت فولاد است و تامین به هنگام یک محموله می تواند کارخانه فولاد را از توقف و تحمل هزینه های سنگین نجات دهد.خوشبختانه در شرایط تحریم واد اولیه آجرهای نسوز عمدتا از خارج از کشور تهیه می شد که باعث خروج ارز از کشور می گردید ولی هم اکنون با انجام آزمایشات متعدد توانستیم فناوری تولید آجرهای نسوز را بومی سازی کرده و آن را در رنج صنعتی تولید نماییم.
شهرستانی با اعلام اینکه در موضوع انتقال مواد نیز اقدامات موثری در صنعت فولاد انجام شده است، تصریح کرد: برای تولید یک تن فولاد ما نیازمندچندین برابر انتقال مواد بودیم. برهمین اساس برای تولید ۳۰ میلیون تن فولاد نیازمند نقل و انتقال ۱۵۰ میلیون تن مواد بودیم که کاملا این موضوع بومی سازی شده است. در بخش الکترونیک، مکانیک و هیدرولیک نیز اقدامات مناسبی جهت بومی سازی نیازمندی ها انجام شده است.
وی اضافه کرد: در تولید فولاد مواد اولیه باید مراحل مختلفی را طی و در نهایت به محصول نهایی تبدیل شوند در این مراحل ما نیازمند ماشین آلات و تجهیزات خاصی هستیم پیش از این بخشی از نیاز ماشین آلات از محل واردات تأمین می شد اما با بومی سازی های انجام شده ما در تمام مراحل انتقال مواد بی نیاز از واردات شده ایم.
این عضو انجمن صنعت فولاد با بیان اینکه در بخش نورد نیز اقدامات مناسبی برای تولید غلتکهای گریز از مرکز دو لایه افقی انجام شده است، افزود: در مجموع صنعت فولاد توانسته است در حوزه بومی سازی مواد مورد نیاز خود اقدامات موثری را انجام دهد حتی ما تمایل داریم تجربه موفق خود را در صنایع دیگر از جمله پتروشیمی ها نیز ارائه دهیم، تا انها نیز از تجربیات و برنامه های ما استفاده کرده و بتوانند در جهت بومی سازی اقدامات موثری را انجام دهند.
در سیستم انتقال مواد اولیه، ترکیبی از یک فیدر نواری، یک توزین دینامیک و یک ماژول کنترلی است که وظیفه آن اندازهگیری و کنترل سرعت تغذیه مواد دانهبندی شده به کوره مطابق با مقدار درخواستی ارسالی از PLC شارژ کوره می باشد. به دلیل وجود ضعفهای موجود در ماژول مذکور از جمله خرابیهای مکرر، دشواری کار با تجهیز به سبب پیچیدگیهای آن، نبود دسترسی به برنامه نرم افزاری اولیه، پایداری کوتاه مدت کالیبراسیون، عدم امکان عیبیابی آنلاین، هزینه زیاد قطعات یدکی و عدم امکان تغییر و بهینهسازی تجهیز، تصمیم بر آن شد که با تکیه بر دانش فنی کارشناسان ناحیه و توانایی شرکتهای داخلی، این ماژول بومی سازی شده است.
شهرستانی با اعلام اینکه قبلاً لجن آهن اسفنجی را به چینی ها می فروختیم، افزود: در حال حاضر که تولید میزان لجن های آهن اسفنجی بالا رفته، خودمان با بدست آوردن تکنولوژی ها این کالا را احیاء می کنیم. اما تعجب من از این است با اینکه ما در قالب برنامه مشخص ضمن افزایش تولید به بومی سازی قطعات و تجهیزات توجه ویژه ای کرده ایم باز به جای حمایت مورد سرزنش قرار می گیریم.
، بومیسازی تولید آهن اسفنجی به روش احیای مستقیم (میدرکس) از دستاوردهای بزرگ صنعت آهن و فولاد کشور است. بهگونهای که متخصصان کشور با بهرهگیری از تکنولوژی میدرکس و با رفع نواقص و ایرادات آن، طراحی، ساخت و نصب کارخانههای احیای مستقیم را بدون نیاز به مشاوره خارجی و با بهترین کیفیت ارائه میدهند. کاتالیستها از جمله مواردی هستند که طی چند سال اخیر و با همت کارشناسان و متخصصان کشور بهطور صددرصد بومیسازی شد و نیاز کشور را به خارج از کشور رفع کرد. هماکنون تعداد انگشتشماری کارخانه تولید کاتالیست ایرانی کل نیاز کشور به این محصول مهم را پوشش میدهند.
ارسال نظر